
|
 |
 |
 |
|
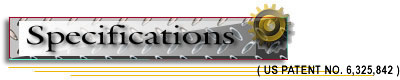
AIRMASTER AERATOR “TURBO” SPECIFICATIONS>
 |
The following specifications cover
the performance, design, construction, and installation of
the floating aeration equipment.
|
 |
Each aerator shall be capable
of producing 3.0 lbs. of oxygen per nameplate horsepower per
hour under normal conditions. Each ____ HP aerator shall be
capable of pumping and mixing approximately 1,908,000 to 12,500,000
gallons per day (depending on horsepower) under normal conditions
and continuous operation.
|
 |
The aerator shall produce two
or four (depending on horsepower) distinct mixing zones within
the lagoon cell for complete mixing of the biomass.
|
 |
The aerator shall have one-third
of the liquid being pumped, directed into a high-pressure
spray. This spray shall be used
for aeration, stripping gases from the liquid, and as a de-foaming
spray.
|
 |
The aerator shall have a synchronous
belt drive system and shaft driven to allow the owner to vary
the speed and performance of the aerator in the field.
A gear box or gear reducer shall not be used.
|
 |
Motor
- The motor shall have the following features:
|
|
- Motor shall comply with EPACT
’92 efficiency standards.
- Service factor of 1.15 to 1.25
(depending on motor type), over the motor nameplate at 60
HZ.
- Class F insulation.
- Double shielded bearings with
re-greasing provisions on the shaft end.
- Motor shall be designed for 230
1-phase or 208, 230 or 460 volt, 3-phase operation.
- Motor shall be IEEE Series 841,
Hostile Duty, or aluminum motor.
|
 |
Frame and Components shall be fabricated of 304-L
stainless steel. A 304-L electrical conduit tray shall be
provided for securing the electrical conduit. Stainless steel
lifting lugs shall be provided for equipment lifting.
|
|
OPTIONAL (for an additional charge)
A NEMA 4 stainless steel electrical junction box shall
be provided with power block, grounding lugs, and pre-wired
to the motor. The junction box
shall allow the electrical contractor to terminate their power
cable from the motor starter.
|
 |
Floatation – to have the following
features:
|
|
- Floats shall be an expanded polystyrene
core with a hybrid urethane coating.
- Coating shall be impervious to
diluted acids, alkalis and petroleum products.
- Floats shall be covered with 304-L
stainless steel expanded metal and designed to support the
weight of two 240 lb. service technicians.
|

|
Impeller shall be of 304-L stainless steel
construction capable of pumping approximately 1,908,000 to
12,500,000 gallons per day (depending on horsepower) under
normal conditions and continuous operation.
The impeller shall be capable of pumping
1 ½” diameter solids.
|
|
Impeller shaft
shall be 1.5” diameter, 17-4 PH 1150 stainless steel
construction.
|
 |
Turbo Blower
shall be 6-blade, 304-L stainless steel construction, capable
of injecting air into the wastewater stream without requiring
a separate motor.
|
 |
Bearings – to have the following
features:
|
|
- Top
bearings to be maintenance free “Double Roller”
pillow block, concentric lock bearings lubricated with a
solid oil lubricant having a load range of 20,200 ft/lbs.
- Bottom bearings to be maintenance
free, Poly-Round Solution® or ALL-ROUND Solution®
, pillow block bearings.
|
 |
Drive system
to be “Poly-Chain GT2® ”.
The toothed, synchronous belt is constructed of non-stretch
material to prevent retensioning.
|
 |
Inlet intake cage shall be of 304-L stainless steel
construction and hinged for ease of cleaning. A 1/4”
stainless steel lifting chain shall be provided.
|
 |
Motor Hood
shall
be of 304-l stainless steel construction. The motor
hood shall cover the motor, drive belt, and the “Double
Roller” pillow block bearings. The motor hood
shall be hinged for ease of access to the above-mentioned
parts with a safety-locking device installed to eliminate
accidental closure of the motor hood. The motor hood
shall be constructed to prevent direct exposure to rain, sleet,
snow, sun, and water spray.
|
 |
OPTIONAL
(for an
additional charge) A 304-L stainless steel standoff assembly
shall be provided for anchoring of the aerator. The stand-off
assembly shall be secured to the lagoon bank through two 304-L
stainless steel spud legs. The other end of the stand-off
assembly shall be connected to the aerator through 304-L stainless
steel receptacles fixed to the end of the frame assembly.
The stand-off assembly allows the aerator to be positioned the
desired distance from the lagoon bank and shall be designed
to allow the operator to move the aerator to the bank for routine
maintenance and inspection. No mooring cables or anchors shall
be required to secure the aerators in position.
|
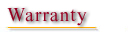
|
The aerator shall be warranted
for defects in materials and workmanship for the period of
one year from date of start-up, or 18 months from date of
shipment, whichever occurs first.
|
|
|
|